Maxon News
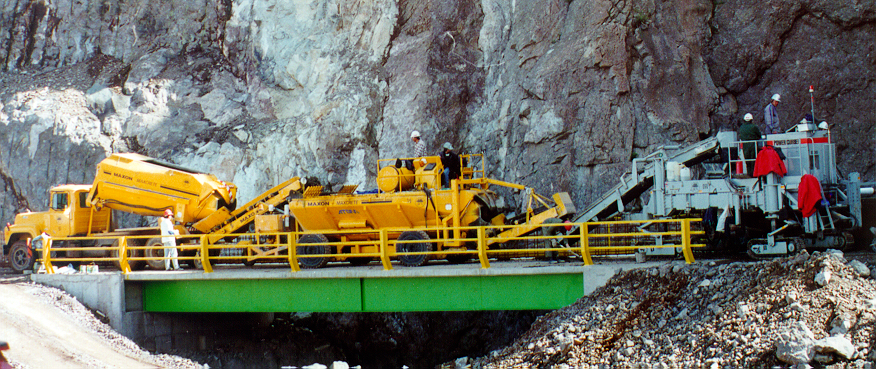
I.C. Vicente Codelco Chile Copper Mine Channel
Truck Mounted Maxcretes and Mobile Maxcrete Build Channel for Chilean Mine
Chilean Contractor Ingenieria Civil Vicente S.A. (ICV) built a channel (sluice) to carry crushed copper ore from inside the mountain to a smelter in the valley. The crushed ore was mixed with water and put in the concrete channel (80 kilometers long at a 1% grade) to flow to the smelter by gravity.
The channel at Codelco’s Minera Andina Mine is located near Los Andes in the Acongaqua Valley, an area principally known for its wine producing vineyards. The mine is also 20 miles from a popular ski resort in the Andes Mountains and 100 miles from Santiago, Chile.
The Challenge
The channel, which was 1.3 meters high by 1.3 meters wide, had been partially hand built with forms by other contractors. However, the process was very slow and the concrete was difficult to deliver to the forms because the channel went inside the mountain and through various tunnels of limited space.
Power Curbers of Salisbury, NC along with ICV, developed a research project to test whether they could slip-form the concrete channel with equipment used for barrier walls. Initial tests were successful with the slip-form paver, except for delivering concrete to the site and feeding the paver in confined spaces.
The Solution
ICV turned to Maxon Industries to design a specialized delivery system to consistently supply concrete to the Power Curber 8700 Slip-form Paver. Maxon proposed a new Mobile Maxcrete and truck-mounted Maxcretes. The Mobile Maxcrete has the unique ability to receive concrete quickly from a concrete truck, remix or re-temper the concrete, and slowly feed the concrete to the slip-form paver in a continuous manner, all while maintaining a low profile. The Mobile Maxcrete’s 10 cubic yard (7.65 cubic meter) surge capacity allows the haul truck to quickly discharge while the Mobile Maxcrete continuously feeds the slip-form paver.Due to the confined space in the tunnel, special Maxon concrete carriers were mounted on the customer’s Mack trucks to quickly discharge the concrete into the Mobile Maxcrete.
With the near vertical walls of the channel, the mix design of the concrete had to be exactly controlled and the slump of the concrete could not vary more than 2 cm. The contractor’s target slump was 4 to 5 cm. The harsh mix with 38 mm maximum size aggregate can be compared to slip-form concrete supplied for airport pavement.
The Concrete Channel
ICV is familiar with slip-form paving, having the first CMI slip-form paver and Hagan Central Mix Plant in Chile. The channel was slip-formed in three separate stages:
Stage 1: The concrete base was laid 5 cm high by 143 cm wide.
Stage 2: Using the same machine with a different mold, the sides of the channel were formed at 1.30 meters high by 1.33 meters wide using 0.8 cubic meters of concrete per linear meter of channel paved.
Stage 3: A special mix of extremely hard aggregates and a high ratio of cement was used for the bottom liner of the channel. The liner was 10 cm high by 75 cm wide because the copper ore was extremely abrasive.
The Equipment
Truck-Mounted Maxcretes
Maxon supplied six (6) low profile 8 cubic yard (6.12 cubic meter) Maxcrete haul bodies mounted on Vicente’s Mack trucks. The units have special full sweep agitators to permit complete discharge of the concrete without hoisting the body. High torque heavy duty Agitator Drives are used so the agitator can turn in extremely harsh and low slump concrete. The truck-mounted units discharge into a newly designed Mobile Maxcrete.
The Mobile Maxcrete
The Mobile Maxcrete can quickly receive concrete from the truck-mounted Maxcrete haul bodies, re-temper or remix the concrete all the while under control slowly discharging the concrete onto a belt conveyor feeding to the Power Curber slip-form unit. The discharge belt conveyor has a radial stacking design which can raise and lower the conveyor, control discharge speed, and swing the conveyor in either direction.
The open-topped 8 cubic yard (6.12 cubic meter) truck-mounted Maxcretes load quickly from the Hagan Central Mix Plant. As soon as a truck-mounted Maxcrete arrived at the paving site, the driver positions the truck to discharge onto the Mobile Maxcrete’s charge belt conveyor and places the truck in neutral. The Mobile Maxcrete, equipped with a pusher frame, then pushed the truck-mounted Maxcrete as it proceeds. This allowed the Mobile Maxcrete operator to match his speed to that of the slip-form paver while simultaneously pushing the truck-mounted Maxcrete. The truck-mounted Maxcrete discharged quickly into the Mobile Maxcrete and departed for the plant for another load.
The Maxon equipment was delivered to Chile in early 1997. The biggest challenge initially was timing the simultaneous dumping of the truck-mounted units, remixing the concrete in the Mobile Maxcrete, and properly feeding the slip-form paver at the correct speed.
However, ICV was able to place over 1,600 linear feet of concrete per day, an 800% improvement from the 197 linear feet per day formed by the previous contractor.
Since the surrounding mountains are rich in copper deposits, other mines may adopt this method of moving ore from the mountain to the smelter. ICV hopes that their success will result in additional contracts at various Chilean mines for many years to come.
Contractor:
I.C. Vicente S.A., Santiago, Chile
Jose A. Vicente Kusanovic (Picture Right) – President
Werner Pieber (Picture Left) – Equipment Manager
Juan Manuel Ibanez – Project Manager
Maxon Distributor:
Atom Santiago, Chile
Arturo Fontecilla Nieto – Sales Manager
Owner:
Codelco-Chile, Division Andina Los Andes, Chile
Ardres Ponce Rojas – Chief Engineer
Salisbury, NC
(704) 626-5871
Download or Print PDF Version: Bul. 369 IC Vicete Codelco Chile Copper Mine Channel
Related posts
Tags
Recent Instagram Posts
Instagram has returned invalid data.Newsletter
Recent posts
-
Maxcrete Remixes Concrete for Chicago Harbor Lock & DamFebruary 29, 2024
-
Factory Refurbished Truck Mounted 12 yd Agitors For SaleFebruary 7, 2024
-
RETC 2023 BOOTH 529 June 11-14thMay 25, 2023
-
Used Truck-Mounted Maxon Agitor For Sale! *SOLD*March 23, 2023